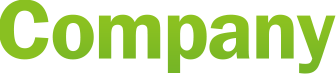
For Health, to Live Better.
Klarity Medical manufactures and distributes a wide range of products that serve the needs of radiation, occupational, hand, and other medical specialists. With facilities in the USA, China, and Europe, Klarity is a world leader in manufacturing and developing thermoplastics and positioning devices. All items are produced with strict ISO 13485 certification and in compliance with all FDA, CE, and other international regulations.
Radiation Oncology
As an expert in radiotherapy patient positioning solutions with two decades of development, Klarity supplies a wide range of positioning and immobilization solutions for various treatment sites and products, including SRS, SBRT, MR RT, Proton Therapy, SGRT, and Overlays.
Physical Rehabilitation
Klarity is one of the most important manufacturers of low temperature thermoplastic splinting materials for 20 years. And now we have expanded our product lines in physical rehabilitation with high temperature thermoplastics, brace and orthosis, intelligent manufacturing solutions for insole customization and compression therapy, etc.
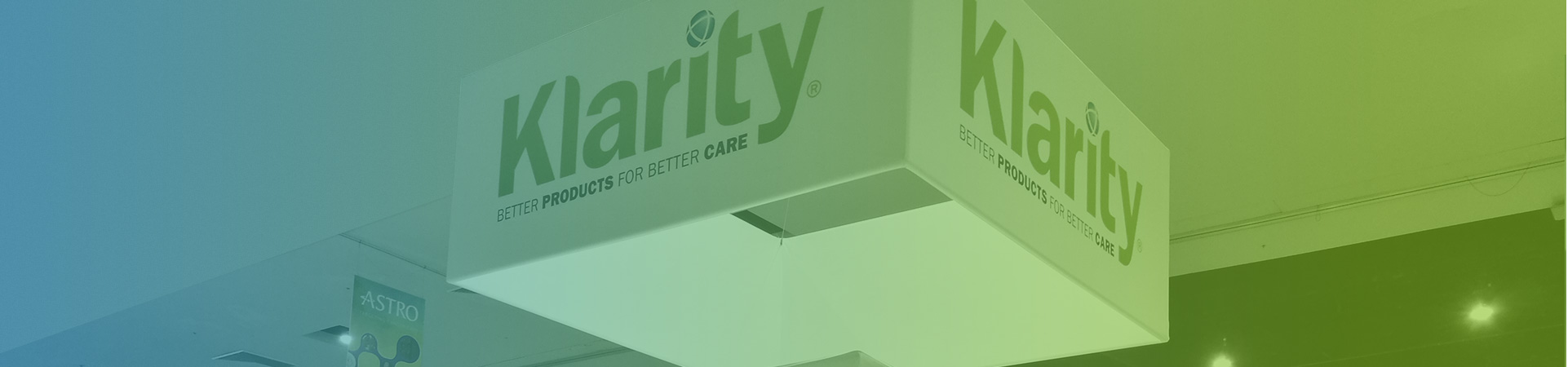
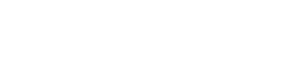

ESTRO Meets Asia, Klarity Meets You – Join Us in Malaysia
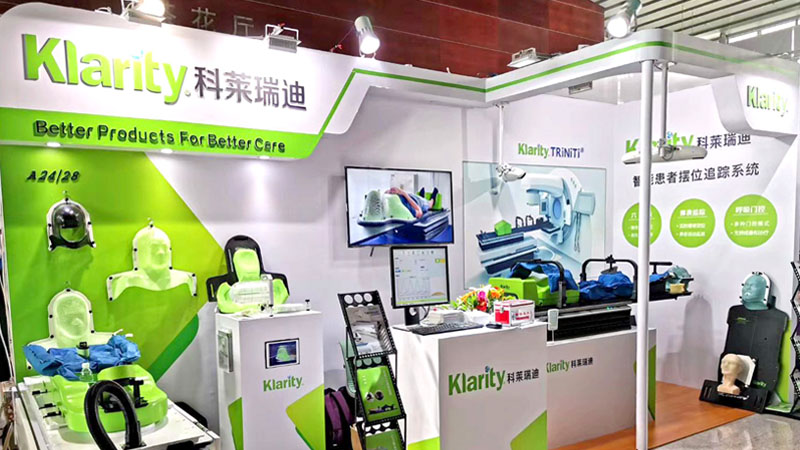
Klarity to highlight Robotic Patient Positioning and Tracking System in 16th CSTRO annual meeting
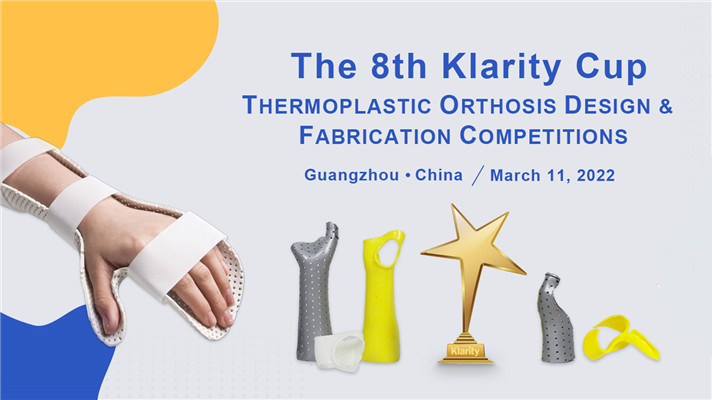
Keep passion! The 8th Klarity Cup Thermoplastic Orthosis Design & Fabrication Competition
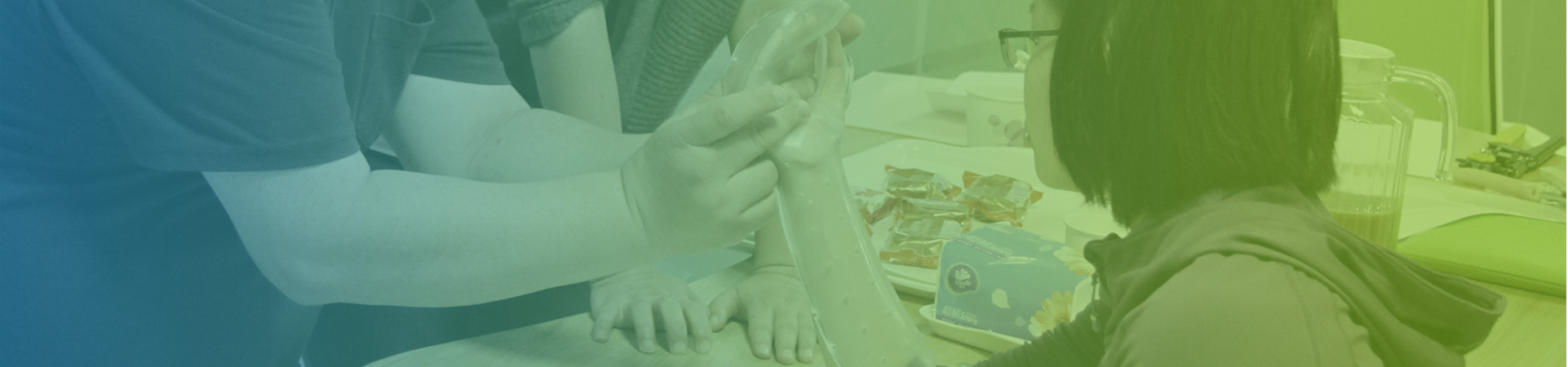
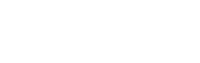
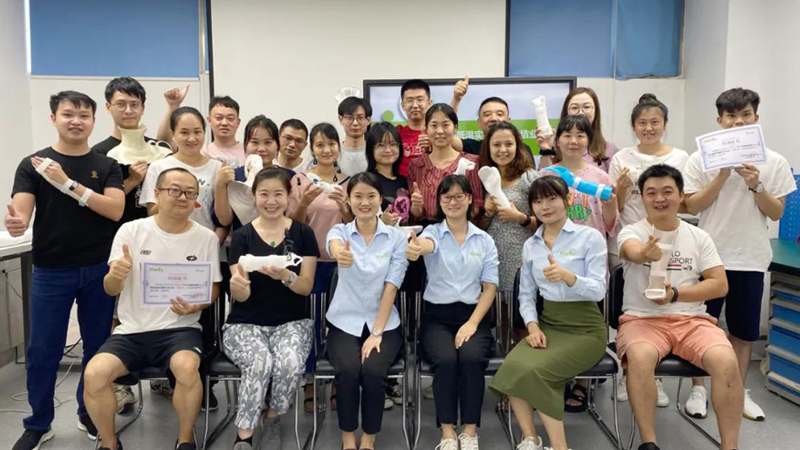
Klarity's 63rd Workshop on Thermoplastic Splinting Successfully Held at Klarity's HQ
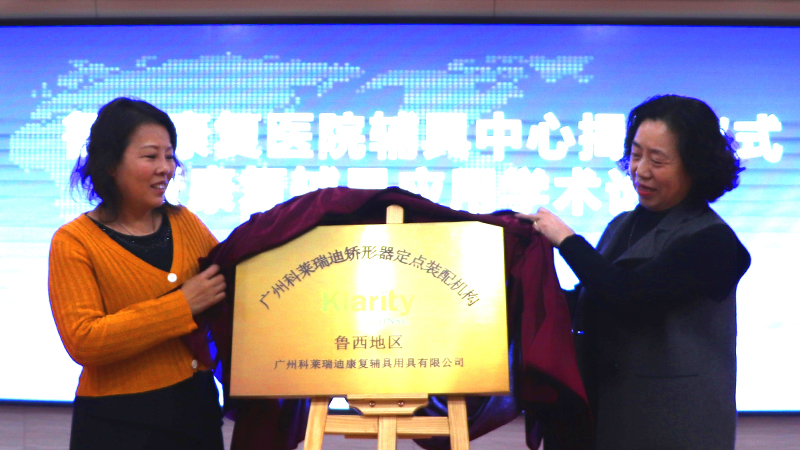
Luxi Rehabilitation Hospital Officially Designated as Klarity's Service Point
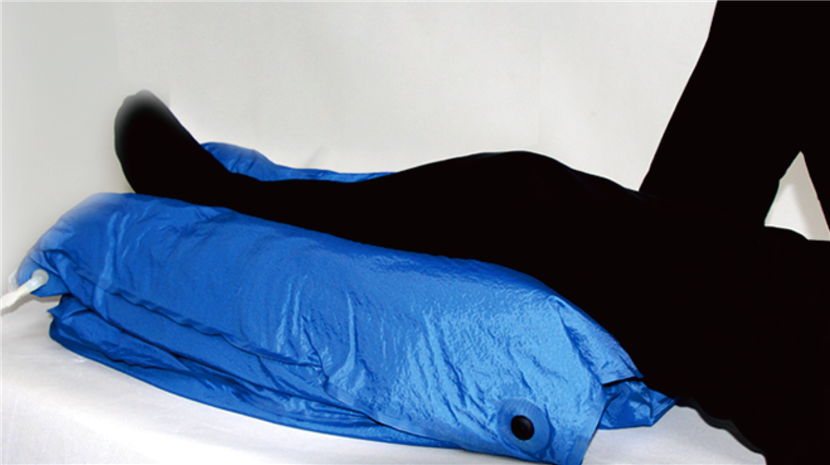
The Extremities Solution: Flexible Limb Immobilization Strategies in Radiation Therapy
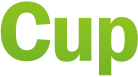
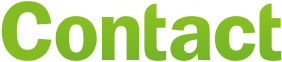
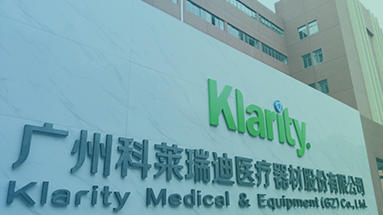
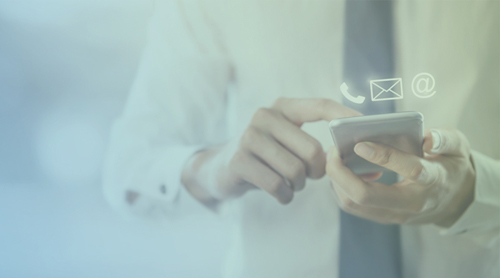

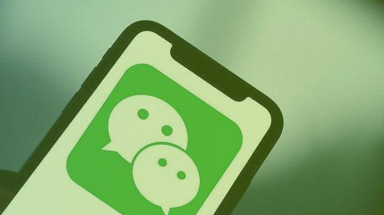

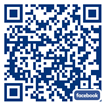
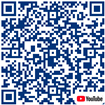
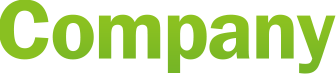


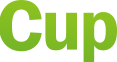